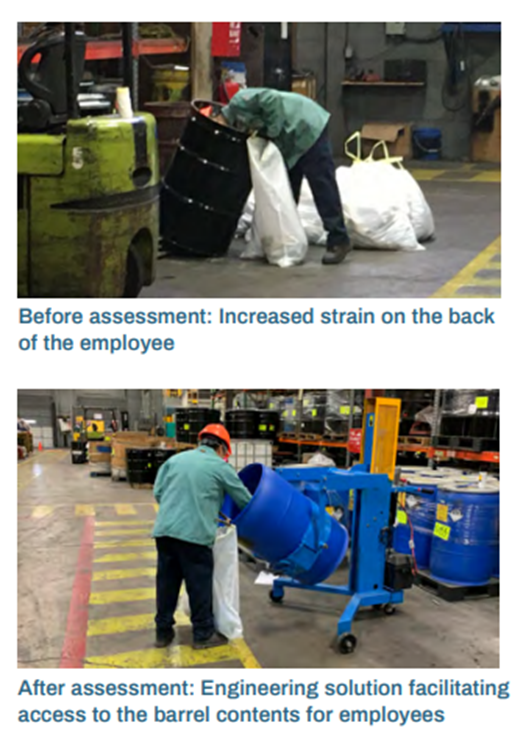
A review of past incidents found that a majority of employee injuries occurred while performing routine job tasks, which represented the majority of recordable injuries. Although these tasks were generally low-risk events, they at times contributed to longer-term injuries that required restrictions in duties.
To improve safety performance, a physical demand analysis was conducted using body movement sensors to analyse stressors while employees completed their tasks. Over three months, more than 100 personal task assessments were completed across the Sims Metal, Sims Lifecycle Services and Sims Municipal Recycling businesses globally.
Through the process, we learned there is no one answer to prevent injuries. A combination of new work environment designs and live coaching is required to reduce task related injuries. Collecting data that verified problem areas for employees enabled Sims to prioritise appropriate actions to target process related risks. Individual coaching was also provided. For example, for de-boxing tasks, this resulted in significant reductions for high load movements per hour in the arm and back. These improvements have and will show sustainable safety performance improvements within the global business.
Learn more here.